OLIN ELECTRIC MOTORSPORTS (FORMULA SAE)
Olin Electric Motorsport is a student-run FSAE team based in Needham, MA. As the current Accumulator Subteam Lead, I manage and mentor a team of 10 engineers, organize subteam meetings, ensuring HV safety, and oversee the project timeline.
Additionally, I am designing and fabricating the 400V battery and working closely with our Electrical subteam for subsystem integration.
Battery Design
The 420V battery powers our electric vehicle.
Final render of a fully assembled segment
I specked out the Molicel P45B Cell and a pack configuration that will allow us to finish the 22km Endurance Race while optimizing for weight and motor controller voltage constraints. The final configuration incorporated insights from performance data from previous events to meet the capacity requirements with a factor of safety.
The final configuration of 6x 102s 4p has a max voltage of 428 V, nominal energy of 6.6 kWh, and weight of 28.5 kg.
Each segment's structure consists of a polycarbonate frame to secure the cells, a power and thermistor board for temperature measurement and cell fusion, handles for quick removal, locating pins to restrict movement, and a touch cover for safety. This final architecture maintains a modular design to minimize risks during integration. Significant time was dedicated to refining the design, as well as the manufacturing and assembly processes, ensuring a well-thought-out approach.
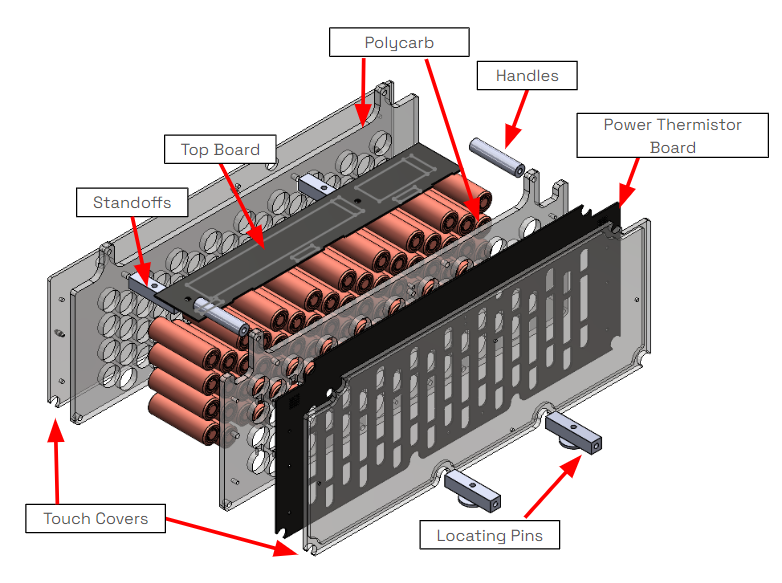
Exploded view of the components of a segment
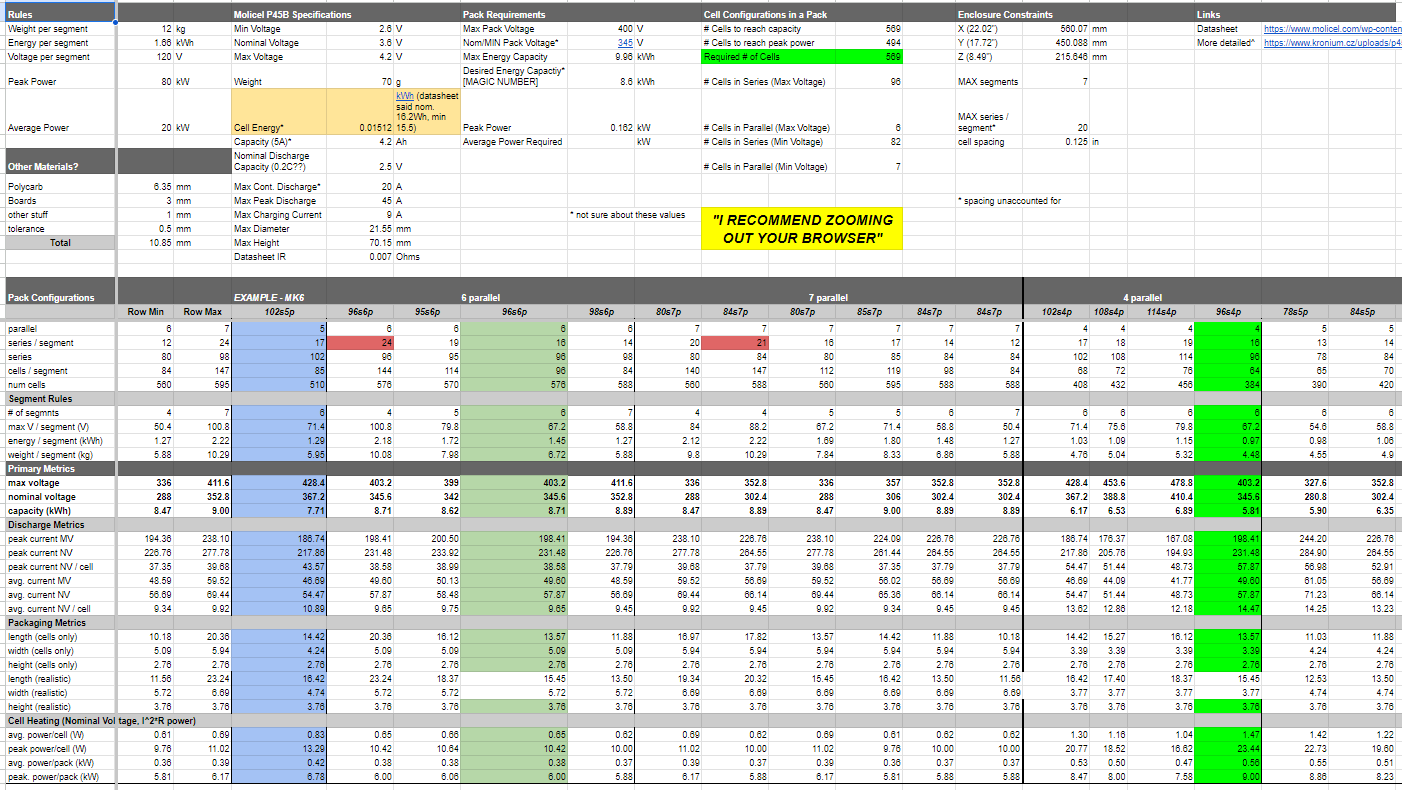
Spreadsheet to automate calculation specs of different configurations
TESTing
Before manufacturing the entire battery pack, a test segment of two parallel cell groups was made to test the mechanical assembly and tolerances of the design. This process allowed us to finalize the press fit tolerances and check the interfacing PCB with the fusible links and cells.
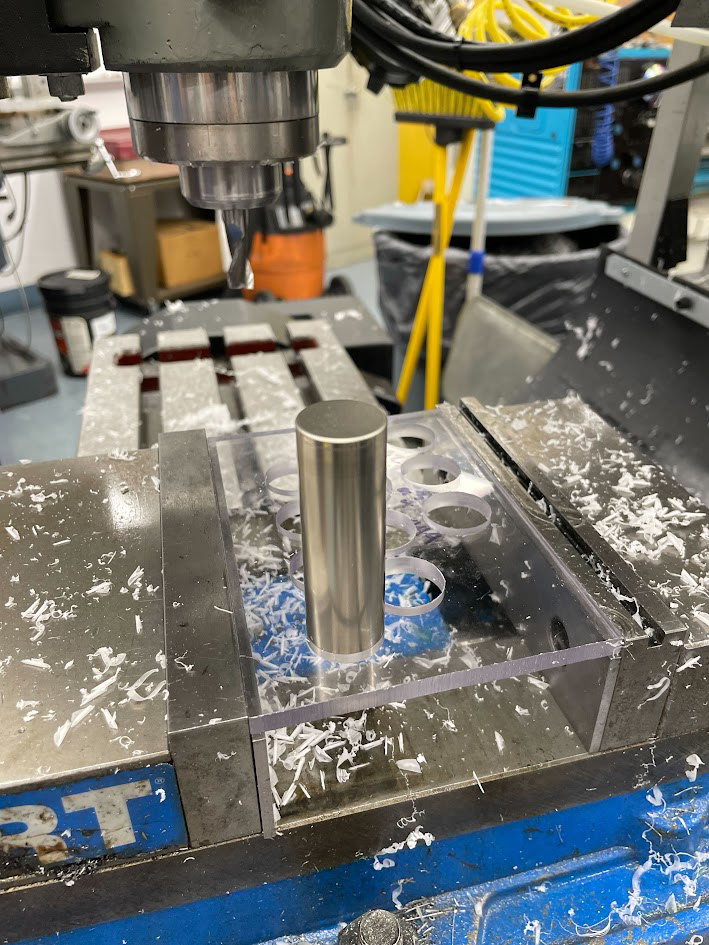
Testing pressfit tolerances
Assembling the mini segment
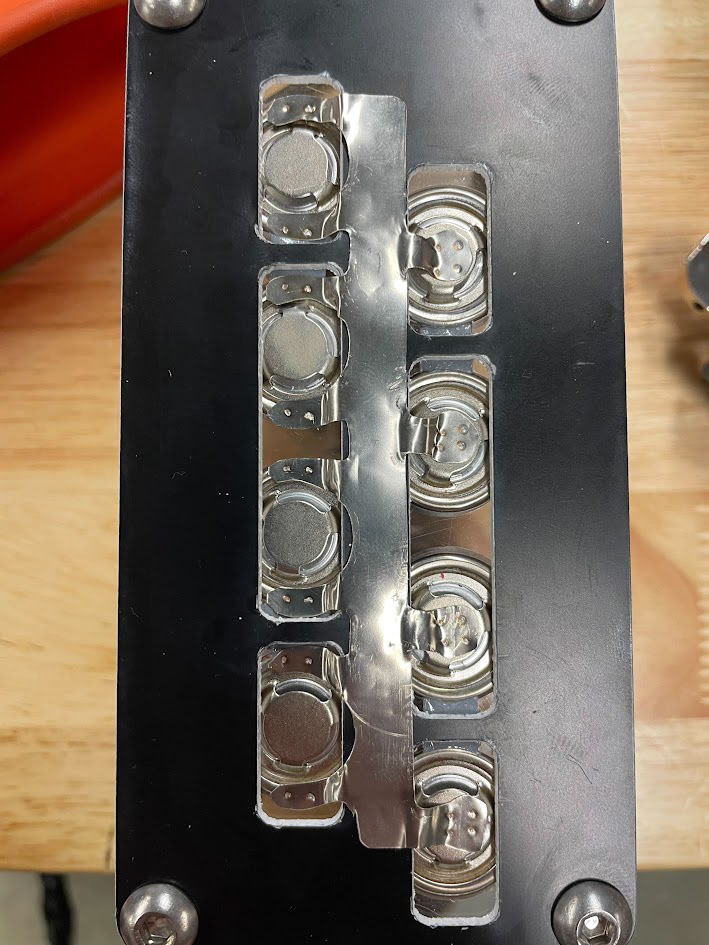
Spot-welding the fusible links
segment Manufacturing
To make the manufacturing process quicker and more consistent, I programed the 3-axis CNC Mill to mill out the parts to the same tolerances. I also designed a manufacturing jig to easily align each sheet of polycarb on the mill.
Securing manufacturing jig
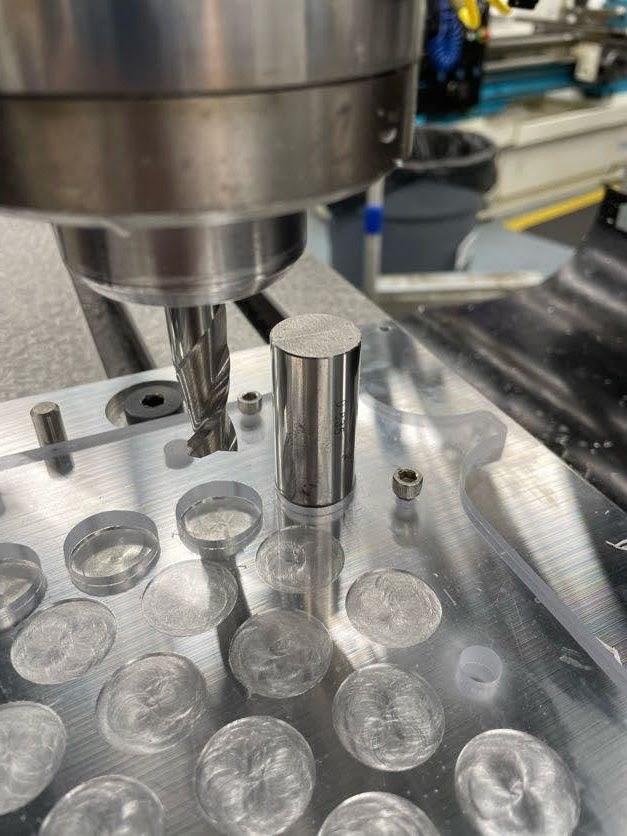
Ensuring right tolerances

Manufacturing on the 3-Axis CNC Mill
segment Assembly
Below is the final mechanical assembly and a video showing the assembly process of a single segment from our battery pack!
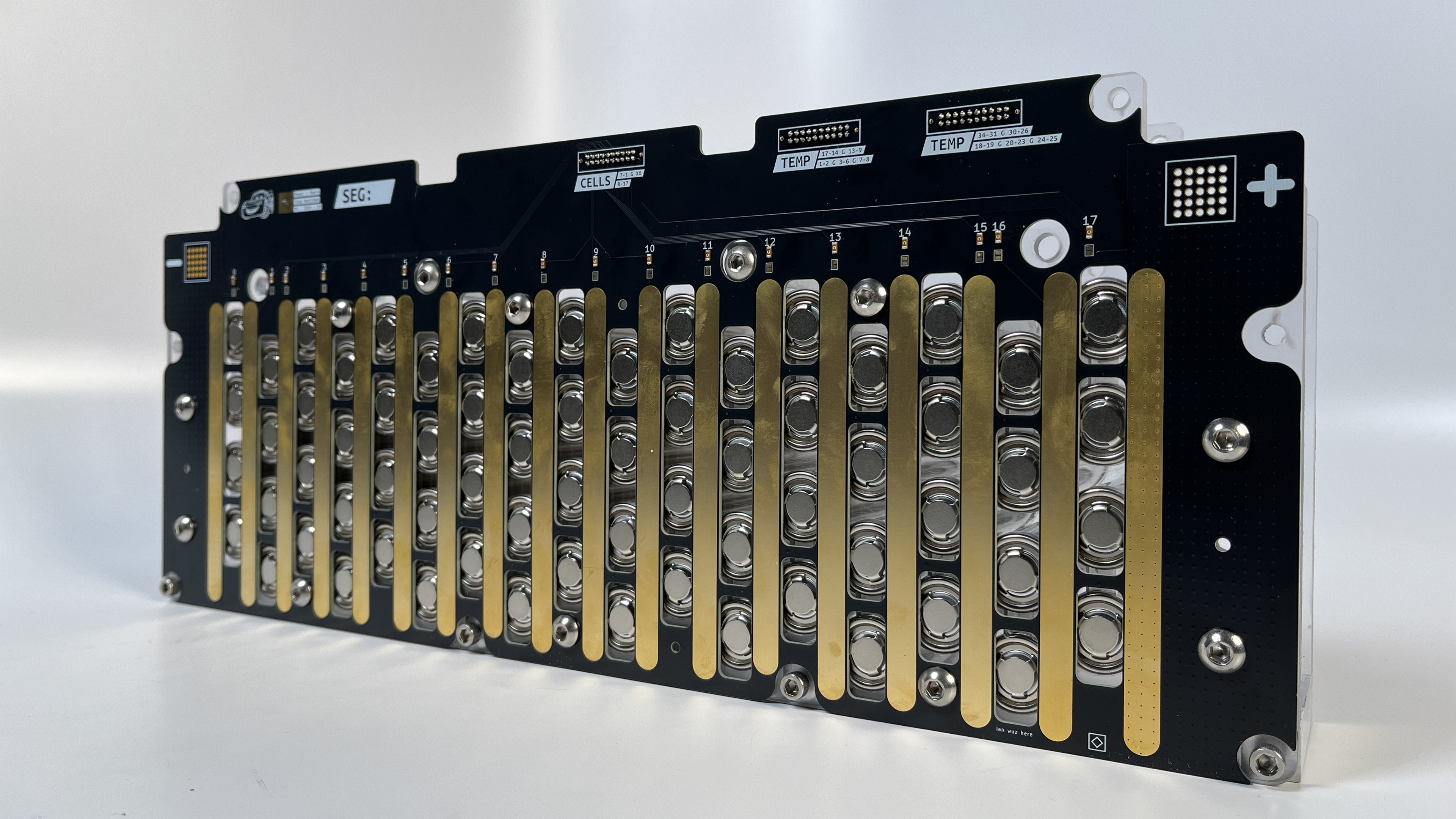
Image of mechanically assembled segment
Waterproofing and material testing
An air-permeable, fire-retardant, and waterproof material.
The final material selected was the Hydrophobic ePTFE Membrane. The testing setup has a replaceable panel inserted to test different materials and a fan mounted in the front. A piece of paper is attached to the other side of the panel while water is drizzled from the front. To test the air-permeability, an anemometer is held on the other side while the fan is powered.
Our vehicle passed the rain test inspection!
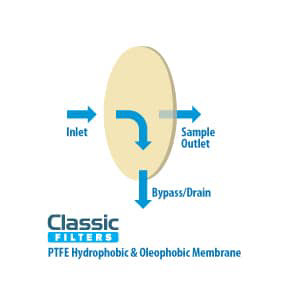
Final material selection
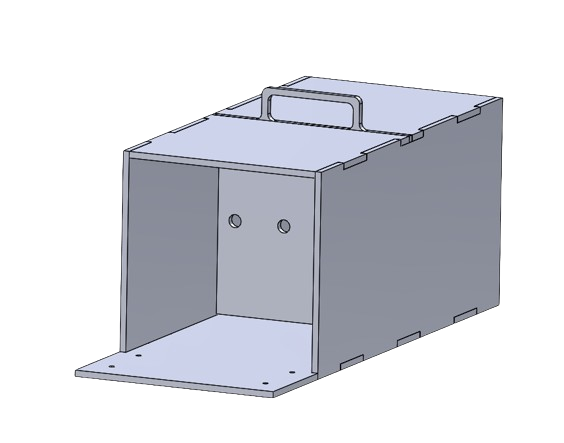
Materials testing setup
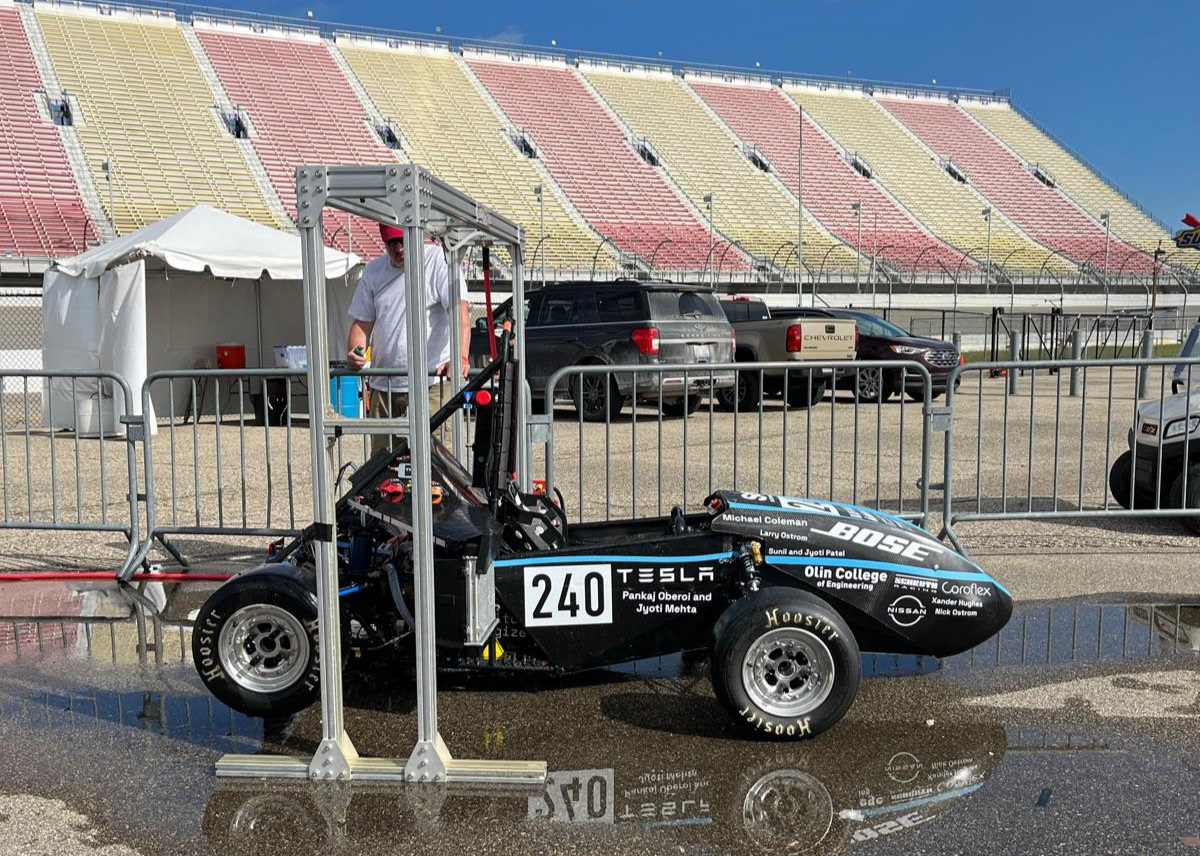
Rain test at the FSAE event in Michigan